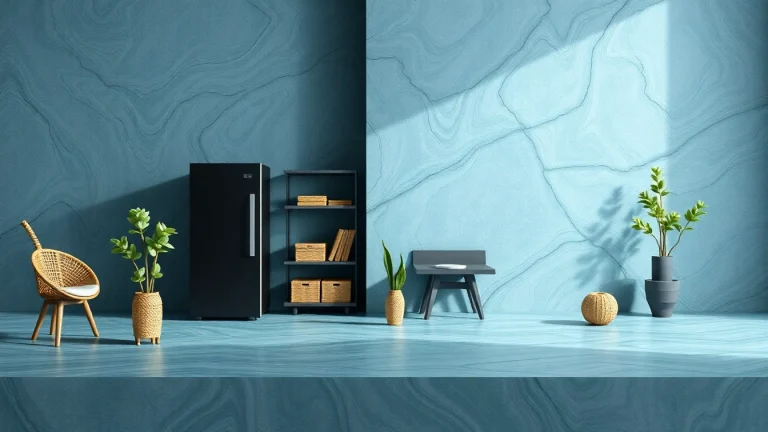
The Leading Liquid Packaging Machine Supplier: Quality Solutions for Your Packaging Needs
Understanding Liquid Packaging Machines
Liquid packaging machines are crucial in various industries, significantly influencing efficiency and product integrity. These machines enable the seamless packaging of liquids ranging from beverages to pharmaceuticals, ensuring that products remain uncontaminated while optimizing production timelines. As businesses strive for operational excellence, the demand for reliable Liquid Packaging Machine Supplier solutions continues to grow.
What Are Liquid Packaging Machines?
Liquid packaging machines are specialized equipment designed to package liquid products into various formats, such as bottles, pouches, and cartons. These machines can handle numerous types of liquids, including viscous substances like sauces, chemical solutions, and even more sensitive fluids like medicines and cosmetics. Turning raw liquids into market-ready products involves several steps, including filling, sealing, and labeling, all of which can be performed either manually or automatically.
Types of Liquid Packaging Machines
Liquid packaging machines vary widely to suit different needs and operational scales. The major types include:
- Filling Machines: These machines are designed to fill containers with precise quantities of liquid. They can be subdivided into several categories, such as gravity fillers, piston fillers, and pump fillers, each offering unique advantages depending on the liquid type.
- Sealing Machines: Sealing is crucial for maintaining product quality. These machines use various methods, including heat sealing, vacuum sealing, and induction sealing, to ensure containers are well-sealed and minimize leakage.
- Labeling Machines: After filling and sealing, products must be labeled accurately. Labeling machines apply adhesive labels to containers, enhancing branding and providing essential information about the product.
- Complete Packaging Lines: Integrated systems combining filling, sealing, and labeling processes into one compact unit. These systems typically increase productivity and streamline operations.
Benefits of Automated Liquid Packaging
Automating the liquid packaging process offers numerous advantages:
- Increased Efficiency: Automated machines can operate continuously, significantly increasing throughput compared to manual labor.
- Cost-Effectiveness: Although initial investment may be high, automation reduces labor costs, improves layout, and minimizes waste.
- Enhanced Accuracy: Automated filling systems ensure consistent volumes, reducing the risk of overfilling or underfilling, which can lead to financial losses.
- Better Safety: Reduces human intervention, minimizing workplace accidents, especially in industries dealing with hazardous materials.
Choosing the Right Liquid Packaging Machine Supplier
Identifying a reliable liquid packaging machine supplier is critical to ensuring that your production processes run smoothly and efficiently. Factors to consider when selecting a supplier include:
What to Look for in a Supplier
The right supplier should demonstrate a comprehensive understanding of the liquid packaging industry. Key attributes to look for include:
- Experience: Suppliers with extensive industry experience can provide valuable insights and tailored solutions.
- Portfolio: A well-rounded product portfolio indicates the supplier’s capability to handle different liquid types and specifications.
- Customer Support: Reliable post-purchase support can significantly reduce downtime in case of technical difficulties.
Evaluating Supplier Reputation
Reputation speaks volumes about a supplier’s reliability and quality. Here are ways to assess a supplier’s reputation:
- Customer Reviews: Look for testimonials and reviews from previous clients on platforms such as Google or industry-specific forums.
- Certifications: Ensure the supplier complies with relevant industry standards and holds necessary certifications, which indicate their commitment to quality.
- Industry Partnerships: Partnerships with recognized organizations can reflect reliability and commitment to innovation and quality.
Important Certifications and Standards
Certifications serve as a benchmark for quality, safety, and compliance. When assessing suppliers, consider whether they possess certifications such as:
- ISO 9001: Indicates a commitment to quality management systems.
- CE Marking: Ensures that products meet European safety standards.
- FDA Compliance: Particularly in food and pharmaceutical industries, FDA compliance is vital to ensure that packaging meets safety and regulatory standards.
Key Features of Modern Liquid Packaging Machines
The evolution of technology has led to the development of sophisticated liquid packaging machines equipped with features that enhance performance and usability. Key features to consider include:
Automation and Efficiency
Modern machines often integrate advanced automation, enabling manufacturers to achieve high efficiency levels. Examples include:
- Smart Sensors: These devices monitor fill levels and other parameters in real-time, allowing for quick adjustments to maintain quality and reduce waste.
- Programmable Logic Controllers (PLCs): PLCs manage machinery operations, enabling complex tasks to be automated with ease.
Safety and Compliance Features
Safety features are paramount in any packaging operation, particularly for volatile or hazardous liquids. Key safety features include:
- Emergency Shutdown Systems: Automatic cut-off mechanisms to prevent accidents in the event of operator error or mechanical failure.
- Leak Detection Systems: Alerts operators to any leaks, protecting both the product quality and the working environment.
Customization Options Available
Different businesses have unique needs based on the products they package. Customization options can include:
- Flexible Size Options: Machines that can handle a range of container sizes accommodate different market needs.
- Variety of Filling Methods: The ability to switch between filling methods enables packaging of numerous liquid types.
Industry Applications for Liquid Packaging Machines
Liquid packaging machines find applications across numerous sectors, each with specific requirements and challenges. Here’s an overview of the primary industries leveraging this technology:
Food and Beverage Industry
The food and beverage industry relies heavily on liquid packaging machines to maintain product quality and safety. Applications include:
- Bottling: Soft drinks, juices, and alcohol are commonly bottled using advanced filling systems that ensure precise volumetric accuracy.
- Pouch Packaging: Soups and sauces are often packaged in pouches to enhance convenience and reduce spoilage.
Pharmaceutical Applications
In the pharmaceutical sector, packaging machines must ensure sterility and product safety. Key applications include:
- Syrup Bottling: Medicinal syrups require precision and compliance with health regulations.
- Vial Filling: Vials used in medication delivery systems necessitate careful handling and filling procedures to avoid contamination.
Chemical and Industrial Uses
The chemical industry uses packaging solutions to contain solvents, detergents, and various liquids. Applications often face unique challenges reflecting the nature of the products, such as:
- Safe Handling: Equipment must withstand corrosive substances and be constructed from appropriate materials.
- Volume Control: Accurate volume control is crucial to reduce waste and manage costs effectively.
Maximizing the Value of Your Liquid Packaging Machine
Investing in advanced liquid packaging machines can provide a strong return on investment if managed wisely. Here are tips on maximizing value:
Maintenance and Support
Regular maintenance is essential to ensure optimal performance and longevity of packaging machines. Tips include:
- Routine Checks: Implement a schedule for regular inspections to identify potential issues before they escalate.
- Professional Servicing: When technical issues arise, seek professional servicing from qualified technicians to minimize downtime.
Training Your Team
Employees must understand how to operate and maintain liquid packaging machines effectively:
- Hands-On Training: Provide training during onboarding processes and ongoing learning opportunities for existing employees.
- Vendor Training Programs: Many suppliers offer training initiatives that can enhance operator skill sets.
Performance Monitoring and Optimization
Analyzing operational performance helps businesses identify areas for improvement:
- Key Performance Indicators (KPIs): Measure metrics such as output rates, downtime, and efficiency levels to develop a clear picture of performance.
- Continuous Improvement Strategies: Implement small tweaks to processes based on data insights to enhance overall productivity and machine reliability.