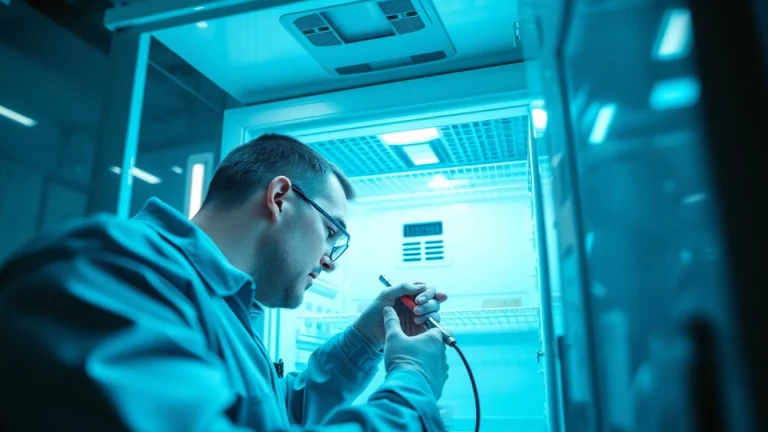
Expert Walk In Freezer Repair: Costs, Solutions, and Maintenance Tips
Understanding Walk In Freezer Repair
Walk-in freezers are essential components in businesses that rely on preserving food and other perishable products. From restaurants to supermarkets, maintaining the integrity of these appliances is crucial for operational efficiency and food safety. However, like any mechanical system, walk-in freezers are prone to breakdowns and require timely walk in freezer repair to remain functional. Understanding the common issues that can arise, the importance of regular maintenance, and knowing when to call a professional are key factors that can save you time and money.
Common Issues and Symptoms
Identifying issues in a walk-in freezer early on can prevent more significant problems down the line. Some common issues include:
- Temperature Fluctuations: If your freezer isn’t maintaining a consistent temperature, it can lead to food spoilage. This can be caused by a malfunctioning thermostat, dirty condenser coils, or issues with the refrigerant.
- Strange Noises: Unusual sounds such as grinding, popping, or buzzing may indicate a problem with the compressor or other mechanical elements.
- Frost Build-Up: Excessive frost can obstruct airflow and efficiency, often due to a faulty door seal or impaired defrost cycle.
- Increased Energy Bills: If your energy costs are rising without a clear reason, it may indicate that your walk-in freezer is struggling to operate efficiently. This could signal a mechanical failure or a need for maintenance.
Importance of Regular Maintenance
Regular maintenance of walk-in freezers is not just recommended; it’s imperative. Routine checks can reveal minor faults before they escalate into costly repairs. Regular maintenance should include:
- Cleaning the Coils: Cleaning both the evaporator and condenser coils can enhance the efficiency and lifespan of the unit.
- Checking Door Seals: Ensuring that door gaskets are intact and functioning properly minimizes heat exchange and enhances energy efficiency.
- Monitoring Temperature: Keeping track of temperature levels ensures that any deviations are addressed promptly, avoiding spoilage and waste.
- Inspecting Electrical Connections: Regular inspection can prevent electrical failures that may lead to costly downtimes.
When to Call a Professional
While minor issues may be resolved through DIY methods, there are times when a professional is necessary. Situations warranting a call to a technician include:
- Persistent Temperature Issues: If fluctuations continue after basic troubleshooting, it’s crucial to consult a technician to avoid food loss.
- Unfamiliar Sounds: Sounds that don’t resolve can indicate a serious compressor or motor issue, warranting professional attention.
- Component Failure: If essential components like compressors or fans fail, only a professional can handle such repairs safely and effectively.
- Refrigerant Leaks: Handling refrigerants requires specialist knowledge and licensing due to environmental regulations.
Cost of Walk In Freezer Repair
Understanding the costs associated with repairing a walk-in freezer helps budget effectively and make informed decisions. Prices can vary widely based on several factors, making it important to evaluate what potential expenses you may face.
Typical Repair Expenses
On average, the cost of walk-in freezer repairs typically ranges from $100 to over $1,000. Here’s a breakdown of common repairs and their estimated costs:
- Compressor Replacement: $250 – $650
- Thermostat Replacement: $100 – $300
- Refrigerant Refill: $150 – $400
- Electrical Repair: $100 – $500, depending on severity
Factors Affecting Repair Costs
Several factors impact the overall costs of repairs, including:
- Age of the Freezer: Older units may need more frequent repairs and might require obsolete parts, increasing costs.
- Type of Issue: Basic maintenance is inexpensive; however, major failures (e.g., compressor issues) are significantly more costly.
- Location and Accessibility: If the walk-in freezer is located in a hard-to-access area, it may increase labor costs.
- Timing: Emergency repairs or services after business hours often incur additional fees.
Cost vs. Replacement Consideration
Sometimes, it’s challenging to decide whether to repair or replace a walk-in freezer. Here are some considerations to take into account:
- Repair vs. Replacement Costs: If repairs exceed 50% of the cost of a new unit, replacement might be the wiser financial choice.
- Energy Efficiency: Older models tend to be less efficient. Newer models can save costs in the long run through reduced energy use.
- Availability of Parts: As models age, parts may become harder to find; this can delay repairs and increase costs.
- Warranty Considerations: New units typically come with warranties, reducing future repair costs.
Choosing the Right Technician for Walk In Freezer Repair
Finding a skilled technician is invaluable in ensuring that walk-in freezer issues are dealt with effectively. A knowledgeable technician can save you time, money, and stress.
What to Look for in a Refrigeration Expert
When selecting a technician for repair services, consider the following:
- Experience and Training: Ensure that the technician has relevant experience and training in commercial refrigeration systems.
- References and Reviews: Positive reviews and testimonials from former clients are indicative of reliable service.
- Licensing and Insurance: Professionals should be licensed and insured to protect against liability during repairs.
- Response Time: Quick response times are critical in a business setting to minimize downtime.
Questions to Ask Before Hiring
Before hiring a technician, asking the right questions can provide insights into their competence:
- What troubleshooting methods do you use?
- Can you provide a detailed estimate before starting the work?
- What warranties do you offer on both parts and labor?
- How do you handle emergencies?
Importance of Certifications
Certifications are critical in determining the competency of a refrigeration technician. Check for certifications such as:
- EPA Certification: Necessary for anyone handling refrigerants, ensuring compliance with federal regulations.
- NATE Certification: North American Technician Excellence certification means they have passed a rigorous testing process in HVAC practices.
- Manufacturer-Specific Training: Training from certain manufacturers can indicate familiarity with specific systems and equipment.
Self-Assessment: Troubleshooting Your Walk In Freezer
Identifying faults in a walk-in freezer can save you time while determining if you need a technician’s help. Here are steps to troubleshoot effectively.
Basic Troubleshooting Steps
- Check the thermostat settings to ensure the temperature is appropriately set.
- Inspect the door seals for any gaps or damage that may cause air leaks.
- Clean the condenser and evaporator coils to enhance cooling efficiency.
- Listen for unusual noises that could indicate mechanical issues.
- Look for any frost buildup in the unit, as this may indicate air flow problems or a fault in the defrost system.
Common DIY Fixes
Several issues can be remedied without professional help. DIY fixes include:
- Replacing Door Gaskets: If the seals are broken, they can be replaced using simple hand tools.
- Clearing Drain Lines: Keeping the drain lines clear can prevent ice buildup.
- Adjusting the Thermostat: Adjusting settings can resolve minor temperature inconsistencies.
Safety Precautions to Take
When attempting repairs or troubleshooting, safety should always be your priority:
- Always turn off power to the freezer before performing maintenance.
- Utilize safety goggles and gloves, especially when dealing with electrical components and refrigerants.
- Read the manufacturer’s manual for specific guidance on maintenance and repairs.
Long-term Maintenance Tips for Walk In Freezers
To avoid costly repairs down the line, implementing a consistent maintenance schedule is essential. Here are actionable strategies:
Seasonal Maintenance Checklist
Seasonal upkeep can help mitigate issues:
- Check and clean condenser coils monthly.
- Inspect door seals and hinges for wear at the start of each season.
- Test the temperature differential of the freezers periodically.
- Ensure defrosting mechanisms are functioning optimally before summer heat sets in.
Energy Efficiency Practices
Enhancing energy efficiency not only helps the environment but also lowers costs. Consider the following:
- Invest in energy-efficient models if replacements are necessary.
- Keep doors closed as much as possible to maintain internal temperatures.
- Regularly maintain and inspect refrigerant levels to maximize efficiency.
Signs Your Walk In Freezer Needs Immediate Attention
Lastly, recognizing when action is urgently required can prevent catastrophic failures. Signs include:
- Sudden massive temperature spikes or drops.
- The presence of water pooling beneath the unit.
- Persistent strange noises despite routine checks.
- Doors that do not close tightly or easily.