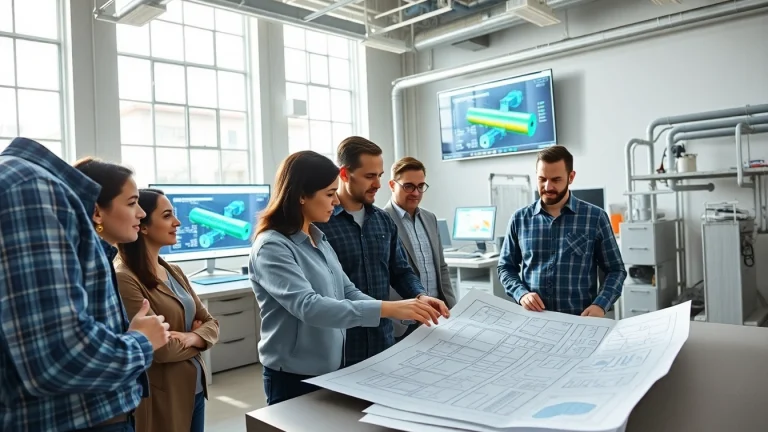
Enhancing Structural Integrity: The Role of a Pipe Stress Analysis Company
Understanding Pipe Stress Analysis
What is Pipe Stress Analysis?
Pipe stress analysis is a systematic approach that engineers use to evaluate the stress levels and performance of piping systems. The goal is to ensure that the pipes can handle the various types of loads they encounter, including internal pressure, temperature changes, vibrations, and external forces such as wind or seismic activity. Through detailed calculations and simulations, this analysis aids in predicting how pipes will behave under operational conditions, ultimately leading to safer and more efficient engineering designs. Established pipe stress analysis company play a crucial role in this field by applying advanced methodologies and technology to deliver accurate results.
Importance of Pipe Stress Analysis in Engineering
The significance of pipe stress analysis cannot be understated. In engineering, safety is the top priority, and improperly designed or analyzed piping systems can lead to catastrophic failures, leaks, or even disasters. For instance, in the oil and gas industry, the financial and environmental repercussions of a piping failure can be staggering. By conducting thorough pipe stress analyses, engineers can identify potential weak points in the design early in the process, facilitating necessary adjustments that enhance system durability and performance.
Key Concepts and Terminology
Understanding pipe stress analysis requires familiarity with several key concepts and terminologies, including:
- Load: Refers to the forces acting on the pipe, including internal pressure, weight of the pipe and contents, thermal expansion, and environmental effects.
- Stress: The internal forces within the material, often expressed in units of pressure (e.g., psi or MPa). Types of stress include axial, bending, and torsional stress.
- Feasibility Study: An analysis phase where potential load scenarios and design specifications are evaluated to determine the overall viability of a piping system design.
- Yield Strength: The maximum stress a material can withstand without permanent deformation, which is crucial for assessing safety margins.
Tools and Technologies Used
Software Solutions in Pipe Stress Analysis
Modern pipe stress analysis relies heavily on software solutions specifically designed for this purpose. Programs such as CAESAR II, AutoPIPE, and AFT Fathom enable engineers to create detailed simulations of piping systems, allowing for accurate stress calculations under varied conditions. These tools offer features like visual modeling, real-time analysis, and compliance checks against industry standards such as ASME B31.3, which governs process piping. By leveraging these sophisticated interfaces, engineers can improve productivity and reduce the likelihood of errors in their analyses.
Data Collection and Analysis Techniques
Effective pipe stress analysis begins with meticulous data collection. Engineers gather information on material properties, pipe dimensions, operating conditions, and layout configurations. Advanced techniques such as laser scanning can be utilized to create a precise 3D model of the existing piping system, which helps in identifying stress distribution more accurately. Once data is collected, it is analyzed using finite element analysis (FEA) methods, which break down complex structures into smaller, manageable components to evaluate their behavior under applied loads.
Innovative Technologies Shaping the Industry
The introduction of innovative technologies is continually transforming pipe stress analysis practices. For instance, the application of artificial intelligence (AI) and machine learning is becoming increasingly prevalent, allowing for predictive analytics that can foresee potential failures before they occur. Moreover, the integration of Internet of Things (IoT) devices in piping systems enables real-time monitoring of stress and strain levels, providing valuable insights that inform maintenance and operational strategies.
Best Practices for Conducting Pipe Stress Analysis
Steps in the Pipe Stress Analysis Process
Conducting an effective pipe stress analysis typically involves a structured series of steps:
- Initial Data Gathering: Collecting specifications, drawings, and material properties that define the piping system.
- Defining Loads: Identifying and categorizing the various forces acting on the system, including internal and external loads.
- Model Development: Building a computer-aided design (CAD) model that accurately reflects the physical layout of the pipes.
- Performing Analysis: Utilizing stress analysis software to assess the model under defined loading conditions.
- Interpreting Results: Analyzing output data, identifying stress concentrations, and comparing the results against allowable limits of stress.
- Recommendations: Providing recommendations for design modifications or reinforcement to address any identified vulnerabilities.
- Documentation: Compiling a detailed report of the findings, methodologies used, and final recommendations for future reference.
Common Challenges and How to Overcome Them
Despite its importance, pipe stress analysis comes with challenges. One major issue is dealing with incomplete or inaccurate data, which can compromise the analysis’s validity. To counter this, engineers should prioritize thorough data verification and validation processes. Another challenge is the complexity of simulations, which might require extensive computational resources. Adopting cloud-based solutions or high-performance computing can help alleviate these demands. Additionally, communication across disciplines (mechanical, civil, electrical) is crucial to ensure that all aspects of the project are aligned, thereby avoiding potentially problematic assumptions in data handling.
Ensuring Compliance and Standards
Compliance with industry standards and regulations is non-negotiable in the realm of pipe stress analysis. Engineers must ensure that their work adheres to relevant guidelines such as ASME, ANSI, and API standards, which dictate the design, construction, and maintenance of piping systems. Regular audits, updates to training, and staying informed about changes in legislation and standards can greatly help companies maintain compliance and uphold quality assurance in their projects.
Case Studies and Applications
Real-World Examples of Successful Pipe Stress Analysis
Learning from real-world applications of pipe stress analysis provides valuable insights into its effectiveness. For example, in a petrochemical plant, thorough pipe stress analysis resulted in the redesign of critical piping areas that were initially deemed high-risk due to thermal expansion. By applying advanced simulation techniques, the engineering team developed a design that not only met safety requirements but optimized the system, resulting in reduced maintenance costs over its lifecycle.
Another notable case involved a large-scale power generation facility. By conducting a comprehensive stress analysis on their cooling water system, the project team was able to identify potential failure points that could arise from fluctuating temperatures and vibrations from nearby equipment. The proactive measures taken not only ensured compliance but also enhanced overall system reliability.
Industry-Specific Applications
Different industries apply pipe stress analysis tailored to their unique operational environments. In the oil and gas sector, stress analysis is critical for offshore platforms, where environmental factors pose significant risks. In the pharmaceutical industry, where sanitary pipelines are essential, precise stress evaluation ensures that processes remain uninterrupted and sterile. Likewise, the nuclear power sector adheres to stringent stress analysis protocols to ensure utmost safety given the high-stakes nature of radioactive materials. Each industry presents specific challenges, benchmarks, and approaches that significantly influence the analysis outcomes.
Lessons Learned from Past Projects
A number of key lessons can be gleaned from past pipe stress analysis projects. First, the importance of interdisciplinary collaboration cannot be overstated; involving team members from various engineering disciplines ensures a rounded perspective on potential challenges. Second, early identification of critical stress points enables better design modifications before construction, preventing costly retrofitting later on. Third, embracing emerging technologies can yield significant efficiency improvements—future-focused companies that start adopting these technologies now will likely enjoy a competitive edge in the market.
Future Trends in Pipe Stress Analysis
Emerging Technologies and Innovations
The landscape of pipe stress analysis is continuously evolving with the emergence of new technologies. For instance, machine learning algorithms are beginning to be applied to predict stress points based on historical data from similar projects. This kind of predictive analytics can provide insights that might be overlooked in traditional analyses, refining forecasting capabilities and ultimately leading to better design choices.
Furthermore, enhanced simulation techniques, such as real-time loading scenarios and dynamic response analysis, offer engineers deeper insights into how piping systems react under various conditions. Innovations in virtual reality (VR) and augmented reality (AR) are also coming into play, providing engineers with immersive environments to visualize and interact with their designs more meaningfully than static models allow.
Sustainability and Efficiency in Engineering Practices
Sustainability is becoming an integral aspect of engineering practices, and pipe stress analysis is no exception. The drive towards more energy-efficient systems has led to the adoption of materials that minimize stress while maximizing durability. Utilizing sustainable design principles in conjunction with thorough stress assessments can significantly reduce the environmental impact of engineering projects while also enhancing their economic viability. Furthermore, incorporating circular economy practices—reusing materials and minimizing waste—further promotes sustainability objectives.
The Future of Pipe Stress Analysis Companies
As industries evolve, so too must pipe stress analysis companies adapt to new challenges and opportunities. Companies that invest consistently in research and development will be better positioned to leverage the latest advancements in technology and methodology. Moreover, expanding service offerings to include comprehensive risk management consultations and advanced simulation services will provide a competitive edge. Finally, future-focused companies must prioritize training their talent to navigate cutting-edge tools and techniques, thereby fostering a culture of innovation that is critical for longevity in an increasingly demanding market.