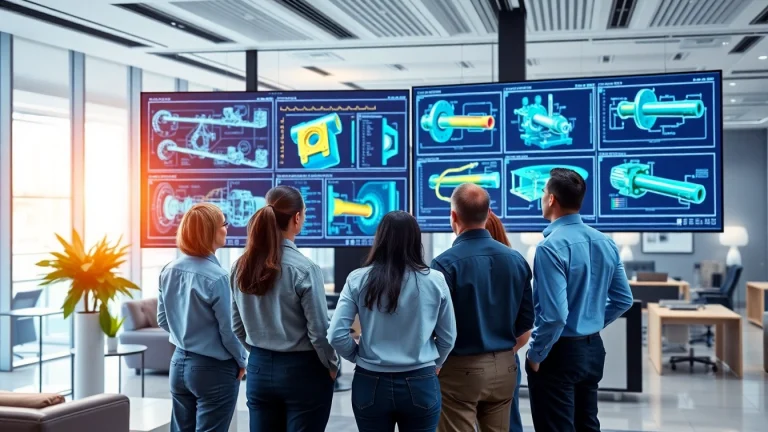
Enhancing Pipeline Integrity: Insights from a Leading Pipe Stress Company
Understanding Pipe Stress Analysis
In industrial settings, pipelines are essential for transporting fluids and gases, making the integrity and functionality of these systems paramount. Understanding pipe stress analysis is critical for ensuring the longevity and safety of these pipelines. pipe stress Company, specializes in evaluating and implementing effective stress analysis techniques that can mitigate risks associated with pipeline failures and enhance operational efficiency.
What is Pipe Stress Analysis?
Pipe stress analysis is a systematic evaluation process used to determine the mechanical behavior of piping systems under various load conditions. This analysis involves assessing the potential deformations, stresses, and failures that pipelines can experience due to internal pressure, temperature changes, weight, and external forces. Engineers utilize specialized software and methodologies to model the pipeline systems accurately, simulating different scenarios to predict performance and identify vulnerabilities.
The Importance of Accurate Calculations
Accurate calculations in pipe stress analysis are crucial for several reasons. Firstly, they help in complying with industry standards and regulatory requirements, which necessitate adherence to safety and operational benchmarks. Inaccurate assessments can lead to inadequate pipeline designs, resulting in leaks, ruptures, or catastrophic failures that pose significant safety hazards and financial losses. Furthermore, reliable stress analysis contributes to the optimization of resources, ensuring that materials used are adequate yet not over-engineered, which can lead to unnecessary expenses. Ultimately, precise calculations empower engineers to deliver durable and efficient piping systems that can withstand operational stresses while maintaining safety.
Common Methods Used in Pipe Stress Evaluation
Several methods are employed in pipe stress evaluation, each serving various applications based on the complexity of the systems being analyzed. The primary methodologies include:
- Analytical Methods: These involve mathematical calculations using hand calculations for simpler systems or pipes. They are commonly used for initial evaluations and smaller projects.
- Finite Element Analysis (FEA): A more advanced and widely used technique that involves discretizing pipelines into smaller segments or elements. FEA provides a comprehensive analysis by simulating how each segment responds to applied loads.
- Computer-Aided Design (CAD) Integration: Modern stress analysis often integrates CAD tools that allow engineers to model pipelines visually and perform stress analysis dynamically within the design environment.
Key Factors Influencing Pipe Stress
Temperature Effects on Pipeline Stress
Temperature changes significantly affect the stress levels in pipelines. As temperatures rise, materials expand, potentially causing thermal stress if the expansion is restrained. Conversely, cooling can lead to contraction, which may introduce additional stresses. Engineers must factor in the maximum and minimum operating temperatures when designing and analyzing pipelines to ensure they can accommodate such fluctuations without failure.
Material Properties and Their Impact
The choice of material for pipes directly influences their performance under stress. Different materials exhibit varying levels of elasticity, tensile strength, and resistance to corrosion and fatigue. For instance, steel pipelines generally withstand high-pressure applications better than plastic pipes but may face issues related to corrosion. Conducting a thorough assessment of material properties helps in selecting the right material, ensuring it can handle the expected loads and environmental conditions throughout its lifecycle.
External Load Considerations
Pipelines do not operate in isolation; they are subjected to various external loads, including soil weight, seismic activity, wind pressure, and even human interference. These loads can exert additional stress on the piping systems, making it crucial for engineers to incorporate these factors into their stress analysis. Utilizing detailed site surveys and risk assessments can help predict external load impacts and design pipelines accordingly. Effective anchoring, supports, and expansion joints can alleviate stress from external sources, enhancing the overall structural integrity of the pipeline.
Best Practices for Pipe Stress Management
Implementing Regular Maintenance Checks
Regular maintenance checks are an essential component of effective pipe stress management. Routine inspections can identify signs of stress-related issues such as cracks, corrosion, and misalignments early before they escalate into more severe problems. An effective maintenance schedule should include visual inspections, pressure testing, and even non-destructive testing techniques for critical pipelines. Keeping detailed records of inspections and maintenance can help track the health of the pipeline system and facilitate timely interventions.
Integrating Technology in Stress Analysis
Modern technology has revolutionized pipe stress analysis. The use of advanced software tools that incorporate simulation capabilities can provide real-time insight into how pipelines react under various conditions. Additionally, technologies such as IoT sensors can be employed to monitor the health of pipelines continuously, providing data that can be analyzed to predict potential failures before they occur. These technological advancements allow engineers to make well-informed decisions and enhance safety protocols significantly.
Training Personnel for Safety and Efficiency
Having well-trained personnel is vital for executing effective pipe stress analysis and management. Companies should invest in ongoing training programs that cover best practices, latest technologies, and safety protocols related to pipe stress evaluation and maintenance. Creating a culture of safety and readiness among employees not only enhances operational efficiency but also fosters a proactive approach to pipeline integrity, minimizing the likelihood of accidents and failures.
Case Studies of Successful Pipe Stress Solutions
Real-World Examples from a Pipe Stress Company
Studying real-world case studies enables engineers to learn from past successes and failures in pipe stress management. One notable example is a major oil and gas company that faced significant challenges with pipeline failures due to thermal expansion. By collaborating with a reputable pipe stress company, they implemented a series of modifications to the existing pipeline system, including the installation of adaptive expansion joints. These changes significantly improved the pipeline’s resilience to thermal stresses, resulting in fewer shutdowns and repairs.
Lessons Learned from Industry Challenges
Industry challenges often provide invaluable lessons. One common issue is improper installation of support systems, which can lead to undue stress concentrations in pipelines. A case involving a mid-sized manufacturing plant resulted in catastrophic failure due to inadequate support placement. Post-incident analysis emphasized the importance of adhering to layout specifications and conducting thorough stress assessments before installation. The lessons learned here reinforced the need for stringent quality assurance protocols in both installation and maintenance processes.
Innovative Solutions in Pipeline Design
Innovative solutions are constantly evolving in pipeline design. Recent advancements have introduced composite materials that offer superior strength-to-weight ratios, enhancing the overall performance while reducing costs. For instance, a company utilizing new composite pipes successfully reduced installation time and minimized strain on their existing systems. This innovation not only eased the construction process but also allowed for better adaptability to environmental changes, showcasing how modern engineering can lead to sustainable pipeline solutions.
Future Trends in Pipe Stress Analysis
The Role of Advanced Simulation Tools
The future of pipe stress analysis will likely revolve around sophisticated simulation tools that can model complex pipeline behaviors under varying operational conditions. Emerging technologies, such as machine learning algorithms, can analyze vast datasets to predict potential stress points and optimize pipeline designs. By employing predictive models alongside real-time data, companies can enhance their preemptive maintenance strategies, leading to improved safety and reduced operational costs.
Predictive Analytics in Pipeline Management
Predictive analytics is poised to transform pipeline management. By leveraging historical data and current operational parameters, predictive analytics can forecast potential stress-related incidents before they occur, allowing for proactive measures. Integrating predictive analytics into maintenance workflows empowers engineers to make data-informed decisions, thereby reducing the risks associated with pipeline stress and increasing overall reliability.
Sustainability Considerations in Pipeline Design
Sustainability is increasingly becoming a priority in pipeline design and management. Engineers are exploring eco-friendly materials and strategies that minimize environmental impact while maintaining structural integrity. Additionally, companies are keen to adopt practices that promote resource conservation, such as recycling materials and utilizing energy-efficient processes during pipeline construction and maintenance. The shift towards sustainable designs helps not only in compliance with regulations but also in enhancing corporate social responsibility.