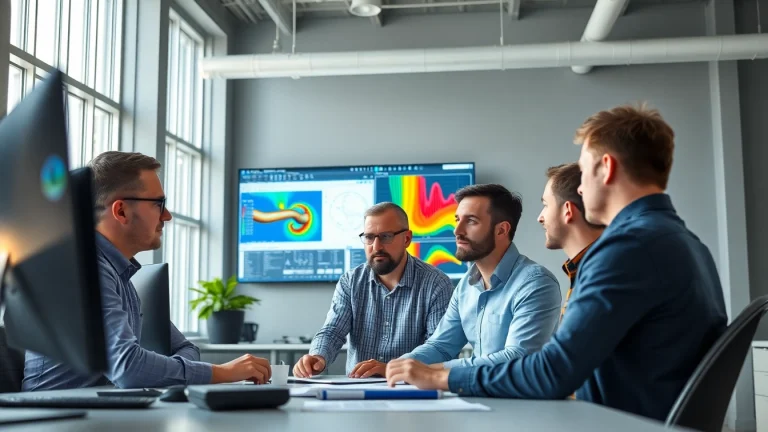
Enhancing Efficiency: Strategies for Pipe Stress Analysis Companies
Understanding Pipe Stress Analysis
What is Pipe Stress Analysis?
Pipe stress analysis is a critical engineering practice that assesses the behavior of piping systems under various loads. This process involves both static and dynamic evaluations to ensure that pipes can withstand the forces they encounter during operation. These forces can originate from thermal expansion, weight of the pipe and its contents, internal pressures, vibrations, and seismic activities. A pipe stress Analysis Company typically utilizes advanced computational methods, such as Finite Element Analysis (FEA), to simulate real-world conditions and provide a comprehensive understanding of potential stresses and deformations that could compromise the integrity of the system.
Importance in Engineering Projects
The significance of pipe stress analysis in engineering projects cannot be overstated. It plays an essential role in designing safe and efficient piping systems that meet industry standards and regulatory requirements. By performing a thorough stress analysis, engineers can:
- Identify potential failure points in the system before construction.
- Ensure compliance with codes and standards such as ASME B31.3 for process piping.
- Reduce the risk of leaks, ruptures, and catastrophic failures, thus improving the safety of operations.
- Optimize support placement and spacing, leading to cost savings in design and construction.
- Enhance the overall lifespan and reliability of the piping systems.
Common Challenges Faced by Pipe Stress Analysis Companies
Pipe stress analysis companies often encounter a variety of challenges that can complicate their assessments, including:
- Complex Geometries: Many installations involve complex shapes and arrangements that can complicate the analysis. Simple models may not accurately reflect the behavior of the completed system.
- Dynamic Load Considerations: The effects of vibrations, seismic forces, and other dynamic loads can be difficult to predict and require sophisticated modeling techniques.
- Data Quality and Availability: Inaccurate or incomplete data about materials, operating conditions, and system configurations can lead to misleading results.
- Regulatory Changes: Keeping up with changes in codes and standards can pose a significant challenge for stress analysis professionals, necessitating continuous updates to methodologies and practices.
Key Techniques in Pipe Stress Analysis
Finite Element Analysis (FEA)
Finite Element Analysis (FEA) is a cornerstone technique used in pipe stress analysis. It allows engineers to create detailed models of piping systems, breaking them down into small elements that can be analyzed individually for stress, strain, and deflection. This method provides several advantages:
- High accuracy compared to traditional hand calculations.
- The ability to simulate complex loading conditions and geometries.
- Visualization of stress distribution across the system, aiding in identifying critical areas that require reinforcement or redesign.
Implementing FEA requires a strong grasp of both the software used and the underlying principles of mechanics, making it an area of ongoing training and development for stress analysts.
Thermal Expansion Considerations
Thermal expansion is a critical factor in the design and analysis of piping systems. Pipes expand and contract due to temperature variations, which can create significant stresses if not properly managed. Engineers need to consider:
- Expansion Loops: These are designed to absorb thermal movement and prevent excessive stress. Proper sizing and placement of loops are vital to efficiency.
- Flexible Joints: These can accommodate movement and reduce stress on the piping system without the need for elaborate supports.
- Material Selection: The choice of materials influences the degree of thermal expansion and contraction. Engineers must balance material strength with thermal properties.
Support Design and Placement
Proper support design and placement are crucial for maintaining the integrity of piping systems. Support locations must be determined based on:
- The weight of the piping, fluid, and any additional equipment.
- The stress caused by thermal expansion and contraction.
- Dynamic loads, including seismic and vibrational effects.
By strategically placing supports and ensuring they are adequately designed to carry loads, engineers can significantly reduce the risk of failure.
Tools and Software for Pipe Stress Analysis
Top Software Solutions
Advancements in technology have led to the development of various software solutions tailored for pipe stress analysis. Some of the leading software tools include:
- CAESAR II: A widely used piping stress analysis software that incorporates comprehensive code checks and user-friendly interface.
- AutoPIPE: This software offers advanced capabilities in dynamic analysis and integrates seamlessly with other design software.
- ANSYS: Known for its powerful FEA capabilities, ANSYS is used to model complex piping systems and analyze their structural performance.
When selecting software, it is essential to consider factors such as user expertise, specific project requirements, and compatibility with other tools in use.
Choosing the Right Tools
Selecting the right software tools for pipe stress analysis is critical for delivering accurate results. Engineers must consider the following:
- Project Scale: Larger projects may require more robust software capable of handling complex systems, whereas smaller projects may need simpler solutions.
- User-Friendliness: Software that is intuitive and easy to navigate allows quicker adaptability and efficient use within teams.
- Support and Training: Access to technical support and training resources can ease the learning curve associated with new software.
- Integration: Tools that integrate well with existing systems can streamline workflows and improve overall efficiency.
Integrating Software into Team Workflow
The integration of software tools into a team’s workflow involves more than just installation; it requires a strategic approach to maximize their benefits:
- Training Sessions: Conducting regular training sessions ensures that all team members are proficient with the tools and can leverage their capabilities effectively.
- Standard Operating Procedures: Developing SOPs that guide how to use the software for specific tasks helps maintain consistency and quality across projects.
- Collaborative Platforms: Utilizing platforms that allow for collaboration within the software encourages knowledge sharing and problem-solving among team members.
Best Practices for Pipe Stress Analysis
Data Accuracy and Validation
One of the most crucial aspects of pipe stress analysis is data accuracy. Poor data can lead to incorrect conclusions and potential failures. It involves several best practices:
- Database Management: Maintain organized databases that include material properties, geometry, and loading conditions for easy reference.
- Quality Control: Implement a robust quality control process to check for data accuracy and consistency before running analyses.
- Use of Sensors: Incorporating sensors in existing systems can provide real-time data that can enhance accuracy during the analysis phase.
Documenting and Communicating Findings
Effective documentation and communication of analysis findings are vital for project integrity and client relationships. Best practices include:
- Clear Reports: Generate comprehensive reports that detail methodologies, findings, and recommendations in an easily understandable format.
- Visual Aids: Use graphics and charts to depict stress distributions and critical points effectively, making it easier for stakeholders to grasp complex information.
- Regular Updates: Provide stakeholders with regular updates on analysis status and findings to maintain transparency throughout the project lifecycle.
Continuous Learning and Development
The field of pipe stress analysis is continually evolving with technological advances and industry standards. Professionals should engage in continuous learning by:
- Professional Development Courses: Enroll in courses that offer advanced training in emerging technologies, software, and methodologies.
- Industry Conferences: Attend industry conferences and seminars to network with peers and gain insights into best practices and innovative solutions.
- Certification Programs: Pursue certifications to validate expertise and stay updated on industry changes and requirements.
Future Trends in Pipe Stress Analysis
Advancements in Simulation Technology
As technology evolves, so do the tools and techniques employed in pipe stress analysis. Future trends suggest a greater reliance on simulation technology, including:
- Real-Time Analysis: Integration of real-time monitoring systems with simulation tools to provide live data for ongoing analysis.
- Artificial Intelligence: AI and machine learning will likely enhance predictive capabilities, allowing for more proactive management of stress analysis.
- 3D Visualization: Enhanced 3D modeling and visualization tools will provide deeper insights into stress distribution and potential failure points.
Impact of Regulatory Changes
The engineering landscape is significantly impacted by regulatory changes. Staying informed about updates is critical, as new regulations often dictate the methodologies used in pipe stress analysis:
- Updated Codes: Familiarizing with the latest codes and standards helps ensure that analyses are compliant and mitigate the risk of legal repercussions.
- Increased Safety Standards: As safety standards become more stringent, analysis methods will need to adapt to meet these requirements.
- Environmental Regulations: Compliance with new environmental laws may necessitate changes in materials and analyses to reduce ecological impact.
Preparing for Industry Shifts
The industry is constantly evolving, and preparation for shifts in demand, technology, or regulatory landscapes is essential for sustainability. Strategies include:
- Flexible Workforce: Develop a workforce adaptable to new technologies and trends, ensuring that the team can pivot in response to changing demands.
- Research and Development: Invest in R&D to explore new methodologies and technologies that can enhance current practices.
- Market Analysis: Conduct regular market analysis to identify emerging trends and adjust business strategies accordingly.