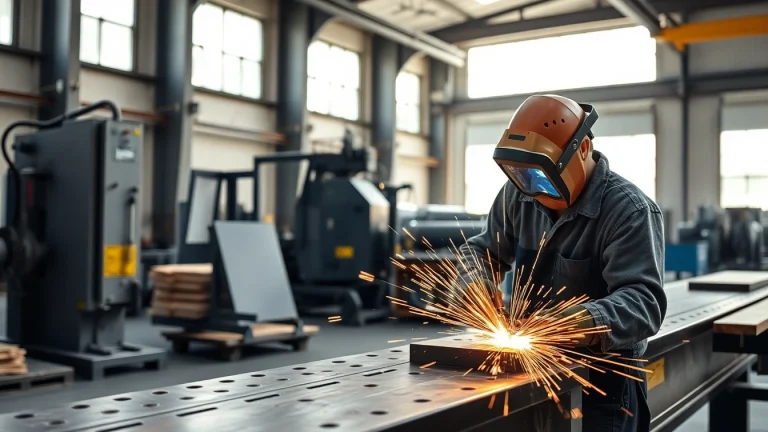
Elevating Standards in Industrial Fabrication Edmonton: Techniques and Innovations
Understanding Industrial Fabrication in Edmonton
Industrial fabrication is a crucial process that serves various sectors, particularly in bustling urban centers like Edmonton. This Canadian city stands out not just for its cultural significance but also for being a key player in the industrial fabrication landscape. Companies involved in industrial fabrication edmonton play an important role in manufacturing and supply chain processes spanning multiple industries. In this article, we will explore the essence of industrial fabrication, its significance within Edmonton, the techniques employed, and the challenges the industry faces today.
What is Industrial Fabrication?
Industrial fabrication refers to the construction and assembly of complex components from various raw materials (such as metal, plastic, and wood) following specific designs and engineering specifications. This subset of manufacturing plays an essential role in producing finished products or parts that serve diverse sectors ranging from construction to aerospace.
The process typically involves several stages, including the design phase, material sourcing, cutting, shaping, welding, machining, and final assembly. The seamless integration of these steps is paramount to achieving high-quality outcomes and operational efficiency.
Key Industries Utilizing Fabrication Services
The industrial fabrication sector spans a multitude of industries. Some of the primary sectors that rely on specialized fabrication services include:
- Construction: Steel beams, columns, and other critical structures are essential for building robust infrastructures.
- Aerospace: Components for airplanes and satellites require precision fabrication to ensure safety and performance.
- Oil and Gas: Custom fabrication supports the installation and maintenance of extraction and processing equipment.
- Automotive: Fabrication processes are critical in manufacturing various vehicle parts, contributing to the overall efficiency and safety of automobiles.
- Furniture and Interiors: Innovative designs often need bespoke fabrication services to realize aesthetic and functional elements.
Due to its rich industrial landscape, Edmonton has solidified its position as a manufacturing hub, making it a favored choice for businesses in these industries to source fabrication services.
The Role of Edmonton in Industrial Fabrication
Edmonton is strategically located in Alberta, boasting a robust transportation network and access to essential resources. This advantageous position enhances its ability to serve various regional orders while facilitating trade and distribution beyond provincial borders.
The city has a legacy of industrial activities that continues to evolve, fostering innovation and adaptation in the fabrication sector. With a rich history rooted in resource extraction and technology development, Edmonton has attracted skilled labor and technical expertise, culminating in advanced fabrication practices. Local businesses invest in state-of-the-art technologies, workforce training, and sustainable practices, further solidifying Edmonton’s stature as an industrial fabrication leader.
Essential Techniques in Industrial Fabrication
Welding Techniques: Types and Applications
Welding is one of the most critical processes in industrial fabrication, enabling the joining of metal parts. The following are common welding techniques utilized in Edmonton’s fabrication sector:
- Arc Welding: A popular method that uses electrical arcs to melt and join metal components. This method includes various types, such as MIG, TIG, and stick welding, each suited for different applications.
- Laser Welding: This innovative technique employs focused laser beams to achieve precise and high-quality welds. It is especially useful for complex designs and thin materials.
- Resistance Welding: Frequently used for smaller components, this technique applies heat generated by electrical resistance to join metal parts. It’s commonly found in automotive applications.
Each welding type has its benefits and ideal applications, impacting the quality of finished products significantly.
Machining: Precision in Every Cut
Machining involves removing material from a workpiece to achieve desired shapes, sizes, and surface finishes. It plays a vital role in ensuring the accuracy of fabricated parts. The following machining techniques are prevalent in the industry:
- Turning: This technique involves rotating a workpiece against a cutting tool to create cylindrical shapes. It is highly useful for producing shafts, bolts, and fittings.
- Milling: In milling, rotating cutters remove material from a stationary workpiece to produce various shapes. It can achieve complex geometries, making it ideal for detailed designs.
- Grinding: This process uses abrasive tools to polish or finish workpieces, enhancing surface quality and tolerances.
Machining allows for high precision and repeatability, essential characteristics in industrial fabrication.
Assembly Processes in Fabrication
The assembly process is integral to fabrication as it brings together the individual components to form a complete product. Different assembly techniques are used based on the complexity and requirements of the project, including:
- Manual Assembly: Workers manually assemble components based on specifications, ensuring thorough quality checks throughout the process.
- Automated Assembly: Involves the use of robots and automated systems, enhancing production speed and accuracy, particularly for high-volume manufacturing.
- Modular Assembly: Components are pre-assembled into modules before being integrated into the final product, allowing for easier assembly and flexibility in design.
Effective assembly processes not only enhance productivity but also ensure that the final product meets quality standards and customer specifications.
Innovations Shaping the Future of Fabrication
Modern Technologies Enhancing Production
The industrial fabrication landscape is continuously evolving, driven by technological advancements. Innovations such as 3D printing, Computer Numerical Control (CNC) machining, and advanced material science are changing the way fabricators approach engineering and production. 3D printing, for instance, allows for rapid prototyping and the manufacturing of complex geometries that were previously unattainable with traditional methods. CNC machining offers high precision and the ability to produce intricate parts efficiently, contributing to increased productivity.
Automation and Robotics in Fabrication
Automation is becoming increasingly prevalent in industrial fabrication, with robots taking on repetitive tasks and enhancing precision. Robotics improves the speed of production while minimizing human error, offering a solution to labor shortages in the manufacturing sector. Common applications include robotic welding, material handling, and quality inspection. As automation technology advances, it is set to revolutionize the workforce landscape by allowing human workers to focus on more complex and value-added tasks.
Sustainable Practices in Industrial Fabrication
Sustainability is becoming a key focus in industrial fabrication, with companies seeking to reduce their environmental footprint and promote green practices. This includes using eco-friendly materials, implementing energy-efficient processes, and minimizing waste during production. Techniques such as lean manufacturing aim to streamline operations and eliminate excess resources, enhancing both profitability and ecological responsibility. As consumers become more environmentally conscious, adopting sustainable practices not only benefits the planet but also enhances brand reputation.
Challenges and Solutions in Industrial Fabrication
Common Issues Faced by Fabricators
Fabricators often face a range of challenges that can impact productivity, quality, and profitability. These challenges include:
- Supply Chain Disruptions: Fluctuations in the availability of raw materials can lead to delays in production.
- Skill Shortages: A lack of skilled labor can hinder operations and innovation in the industry.
- Quality Control Issues: Inconsistent quality can result from inadequate testing processes or poorly designed components.
Adaptive Strategies for Success
Addressing these challenges requires strategic planning and adaptive measures. Here are some effective approaches:
- Diversifying Suppliers: Building relationships with multiple suppliers can mitigate risks associated with supply chain disruptions.
- Investing in Training: Offering regular training and development programs can enhance workforce skills and retention.
- Implementing Robust Quality Assurance Systems: Establishing stringent quality control measures at each production stage can drastically reduce defects and inconsistencies.
Case Studies of Overcoming Challenges
Several Edmonton-based companies exemplify successful adaptations. For instance, a local metal fabrication firm faced supply chain issues due to global disruptions. By diversifying its supplier base and investing in local sourcing, it managed to reduce lead times significantly. Another case involves a fabrication company that implemented comprehensive employee training programs, resulting in reduced turnover rates and improved production quality. These real-life examples illustrate practical strategies that fabricators can adopt to navigate common industry challenges.
Measuring Performance in Industrial Fabrication
Key Metrics for Success
Measuring success in industrial fabrication requires monitoring specific performance metrics. Key performance indicators (KPIs) typically include:
- Production Efficiency: This metric indicates how effectively resources are utilized, often calculated as the ratio of outputs to inputs.
- Product Quality: The number of defects or customer complaints related to product quality can serve as a benchmark for performance.
- On-Time Delivery: This measures the percentage of orders shipped by the agreed timeframe, reflecting overall operational effectiveness.
Quality Control Processes
The quality control process is essential in ensuring that the final products meet or exceed industry standards. This involves conducting inspections at various stages of production, utilizing statistical methods to monitor process effectiveness, and engaging in regular audits. Ensuring quality not only enhances customer satisfaction but also reinforces a company’s reputation in the industry.
Client Feedback and Continuous Improvement
Client feedback plays an integral role in continuous improvement efforts. Regularly soliciting feedback helps firms identify areas for enhancement and innovation. Implementing customer suggestions into the production process can lead to product improvements and greater customer loyalty. Furthermore, establishing a culture of continuous improvement encourages employees to innovate and adapt, positioning the company for long-term success.