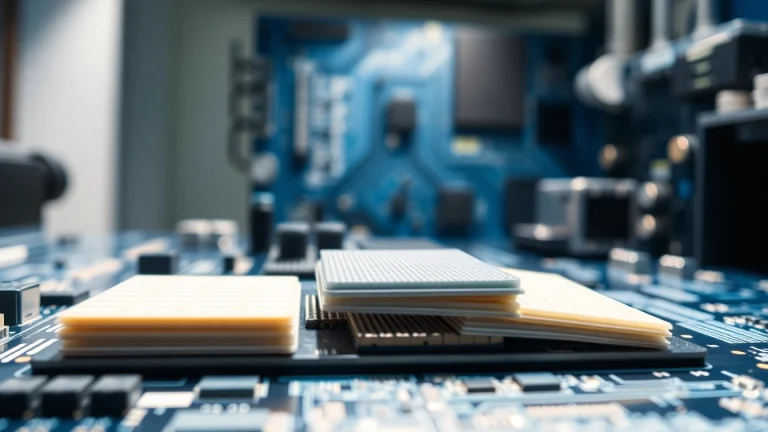
Understanding Thermal Management Materials: Key Types and Applications
1. Introduction to Thermal Management Materials
In the world of electronics, thermal management materials play a crucial role in ensuring device reliability and performance. These materials are assorted types that effectively dissipate heat generated by electronic components, particularly in high-performance applications where overheating can lead to failure. Whether in computers, smartphones, electric vehicles, or industrial machinery, managing excess heat is vital. Understanding thermal management materials and their applications is key to optimizing the performance and longevity of modern electronic devices.
1.1 What are Thermal Management Materials?
Thermal management materials encompass a variety of substances designed to facilitate the transfer of heat away from sensitive electronic components. These materials can be categorized into thermal interface materials (TIMs), thermal gap pads, adhesives, gels, and more. Each material serves a specific function within electronic applications, including heat dissipation, thermal insulation, and enhancing heat conduction. By effectively managing thermal energy, these materials help maintain optimal operating temperatures and prevent prolonged heat exposure that could damage components.
1.2 Importance of Thermal Management in Electronics
The importance of thermal management in electronics cannot be overstated. As devices become more powerful and compact, the heat they generate also increases. Effective thermal management helps in:
- Enhancing Performance: Proper heat dissipation allows electronics to function at their designed performance levels without throttling caused by overheating.
- Extending Lifespan: Cooling solutions help in reducing wear on components, thereby extending their operational life and reliability.
- Safety: High temperatures can lead to component failure, posing risks of fire or damage to surrounding components.
- Compliance: Many industries have stringent regulations regarding thermal performance, driving the need for effective thermal solutions.
1.3 Overview of Key Applications
Thermal management materials are employed across various sectors, including:
- Consumer Electronics: Smartphones, tablets, and laptops utilize thermal management solutions to ensure optimal functioning during intensive operations.
- Automotive: Electric vehicles rely on advanced thermal management solutions to regulate battery and engine temperatures.
- Industrial Equipment: Machinery and electronic systems used in manufacturing require efficient cooling to ensure continuous operation and reduce downtime.
- Telecommunications: Network equipment must manage heat generation to maintain reliable data transmission and device longevity.
2. Types of Thermal Management Materials
Understanding the various types of thermal management materials enables engineers and designers to select the appropriate materials for their specific applications. Here, we explore some common categories of thermal management materials.
2.1 Thermal Interface Materials (TIMs)
Thermal Interface Materials are vital for eliminating air gaps between surfaces that need efficient heat transfer. Common types of TIMs include:
- Thermal Greases: These viscous compounds improve thermal conductivity between surfaces and are commonly used in processors and high-power LEDs.
- Thermal Pads: Soft, conformable pads that fill gaps and provide good thermal conductivity while being easy to apply.
- Thermal Adhesives: These materials facilitate heat transfer while also securing components together.
2.2 Thermal Gap Pads and Adhesives
Thermal gap pads and adhesives serve to bridge the gap between components while effectively conducting heat. They are typically made from polymer composites and are designed for different thermal conductivity requirements. Features include:
- Conformability: Many gap pads can adjust to the surface irregularities, ensuring maximum contact area and heat transfer.
- Electrical Insulation: Some types also provide electrical insulation, making them suitable for use in sensitive electronic applications.
2.3 Thermal Gels and Pastes
Thermal gels and pastes are often used in applications where high thermal performance is required. These materials are typically composed of syntactic materials that provide superior thermal properties to either thermal greases or pads. Key characteristics include:
- Enhanced Thermal Conductivity: Thermal gels often offer higher thermal conductivity than traditional greases.
- Easy Dispensing: Many gels can be dispensed easily, making them suitable for automated production.
- Wide Temperature Range: Often rated for extreme temperatures, making them appropriate for high-performance applications.
3. How to Choose the Right Thermal Management Material
Selecting the right thermal management material is essential for ensuring efficient heat transfer and optimal device performance. Here are the key considerations to keep in mind while making your selection.
3.1 Evaluating Thermal Conductivity
Thermal conductivity is one of the most critical properties of thermal management materials. Higher values indicate better heat dissipation capabilities. When selecting materials, it is crucial to assess:
- Material Type: Different materials exhibit varying thermal conductivities; for instance, metals usually perform better than polymers.
- Operating Condition: Consider the operating temperature range and frequency of thermal cycling that the material will endure.
3.2 Considerations for Material Compatibility
Ensuring compatibility between the thermal management material and the components it’s interfacing with is vital. Factors include:
- Chemical Stability: Verify that the material won’t degrade or react adversely with other materials.
- Mechanical Properties: The selected material should possess adequate mechanical properties for the application (e.g., not compressing excessively under pressure).
3.3 Environmental and Regulatory Factors
Environmental impact and regulatory standards can also dictate the choice of thermal management materials. Key considerations include:
- End-of-Life Disposal: Materials should be chosen based on their environmental impact and recyclability.
- Regulatory Compliance: Especially in electronics, materials must comply with specific regulations (such as RoHS, REACH).
4. Best Practices for Implementing Thermal Management Solutions
To maximize the performance of thermal management materials, it is essential to follow best practices during implementation. Here are effective strategies to keep in mind:
4.1 Installation Techniques for Optimal Performance
Proper installation of thermal management materials is crucial for achieving effective heat dissipation. Key techniques include:
- Surface Preparation: Ensure that the surfaces are clean, dry, and free from contaminants that could affect adhesion.
- Uniform Application: Apply materials evenly to avoid air pockets or gaps that could impair thermal conductivity.
- Pressure and Compression: Ensure that the materials are compressed adequately to maximize contact area.
4.2 Performance Testing Methods
To verify the effectiveness of the thermal management solution, conduct performance tests, including:
- Thermal Imaging: Use infrared cameras to visualize heat distribution and identify hotspots.
- Temperature Profiling: Measure temperature differential across the assembly to assess effectiveness.
- Long-Term Testing: Evaluate performance over extended periods under normal operating conditions.
4.3 Common Pitfalls to Avoid
Avoiding common mistakes can significantly enhance the effectiveness of thermal management solutions. Key pitfalls include:
- Underestimating Heat Load: Failing to account for all heat sources can lead to inadequate cooling solutions.
- Neglecting Material Properties: Using materials without considering their thermal and mechanical properties can lead to failure.
- Ignoring Environmental Conditions: Not considering ambient conditions (temperature fluctuations, moisture, etc.) might impact the performance.
5. Future Trends in Thermal Management Materials
As technology advances, the demand for more efficient thermal management materials will drive innovation. Here, we explore upcoming trends and anticipated changes within the field.
5.1 Innovations in Material Science
Innovative materials are expected to emerge, focusing on enhancing thermal conductivity while optimizing costs and ease of application. Some anticipated developments include:
- Nanomaterials: The introduction of nanomaterials that can exhibit enhanced thermal properties.
- Phase Change Materials: These materials absorb and release heat as they transition through phases, capable of providing efficient thermal cycling.
5.2 Impact of Emerging Technologies on Thermal Solutions
Technological advancements such as the rise of AI, IoT devices, and electric vehicles will continue to shape the requirements for thermal management solutions. Key impacts include:
- Increased miniaturization: As electronic devices become more compact, the demand for advanced thermal management solutions will escalate.
- Higher Power Densities: Emerging technologies will necessitate solutions capable of dissipating heat from higher power systems effectively.
5.3 Predictions for Market Growth and Potential Challenges
The global market for thermal management materials is projected to experience substantial growth, as industries seek reliable solutions for managing heat. Challenges may include:
- Material Sourcing: Ensuring the availability and sustainability of raw materials will be crucial in meeting demand.
- Technology Integration: It can be challenging to integrate new thermal management solutions into existing manufacturing processes effectively.