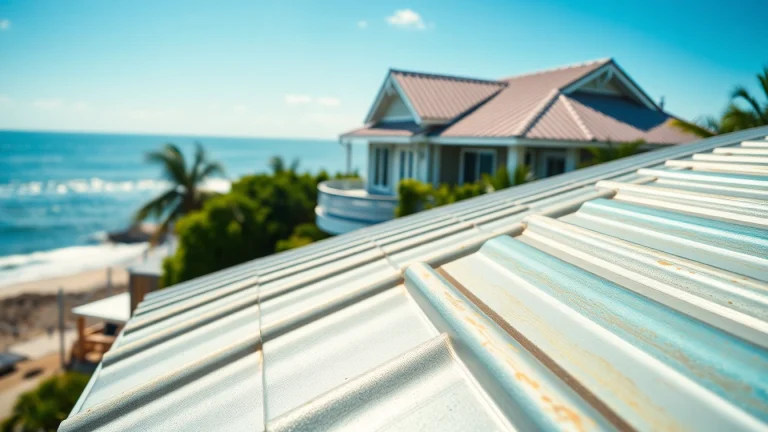
Comprehensive Guide to Coastal Metal Roofing: Benefits, Installation, and Maintenance
Understanding Coastal Metal Roofing
Coastal areas are uniquely beautiful but also present distinctive challenges for homeowners, especially when it comes to roofing. Due to their exposure to salty air, strong winds, and moisture, traditional roofing materials often falter over time. Enter coastal metal roofing, a highly resilient choice that is gaining popularity among coastal homeowners. In this article, we will delve into the intricacies of coastal metal roofing, exploring its benefits, materials, installation processes, maintenance guidelines, and cost implications, providing a comprehensive guide for homeowners and contractors alike.
What is Coastal Metal Roofing?
Coastal metal roofing refers to roofing systems specifically designed to withstand the harsh conditions typical of coastal environments. Typically made from materials such as aluminum and galvanized steel, these roofs feature protective coatings that resist corrosion and weathering caused by salty sea air and humidity. Additionally, coastal metal roofs can take various forms, including standing seam, corrugated panels, and shingles, each offering unique aesthetic and functional advantages.
Benefits of Choosing Coastal Metal Roofing
The advantages of opting for coastal metal roofing extend beyond just aesthetic appeal. Here are some compelling benefits:
- Durability: Coastal metal roofs have high resistance to wind, rain, and salt, making them ideal for areas prone to hurricanes or tropical storms.
- Longevity: The typical lifespan of metal roofing can reach 50 years or more when properly maintained, outperforming many traditional roofing materials.
- Energy Efficiency: Many metal roofs reflect solar radiant heat, which can reduce your cooling costs significantly compared to traditional asphalt shingles.
- Environmentally Friendly: Metal roofing materials are often made from recycled materials and can be recycled at the end of their lifespan, which is a more sustainable option compared to asphalt roofing.
- Low Maintenance: Coastal metal roofs should require minimal maintenance compared to other types of roofs, as they are less likely to succumb to mold and mildew.
Common Materials Used in Coastal Metal Roofing
Several types of materials are popular in the construction of coastal metal roofs, each with their own unique properties:
- Aluminum: Known for its lightweight nature and excellent corrosion resistance, aluminum is a preferred choice in highly saline environments.
- Galvanized Steel: This steel is coated with a layer of zinc, which protects it from rust and corrosion, making it a cost-effective solution for metal roofing.
- Zinc: Like aluminum, zinc is naturally resistant to corrosion but is often chosen for its unique patina that develops over time, giving it a distinctive look.
- Galvalume Steel: A further enhancement of galvanized steel, Galvalume features a combination of aluminum and zinc coatings, providing superior durability and corrosion resistance without sacrificing strength.
Factors to Consider for Coastal Metal Roofing Installation
Local Weather Conditions Impacting Installation
Before beginning installation, it is crucial to consider geographic factors. Coastal regions generally experience increased humidity, salt spray, and hurricane winds. Understanding your local climate will guide your choice of roofing materials, installation methods, and ventilation systems.
Choosing the Right Roofing Contractor
Working with a skilled contractor who has experience in installing coastal metal roofs is imperative. They should understand local building codes, particularly those specific to coastal areas, which may differ significantly from inland regulations. Look for contractors with a solid track record and positive reviews from previous customers.
Permitting and Regulations for Coastal Areas
Coastal regions often have stringent building codes and zoning regulations aimed at protecting properties from extreme weather events. Homeowners should familiarize themselves with any required permits to ensure compliance and avoid potential fines during the installation process.
Installation Process for Coastal Metal Roofing
Preparation and Planning Stages
The first step in the installation involves thorough planning and preparation. Homeowners and contractors should assess the existing roof structure, determine the type of metal roof suited for the environment, and draft an installation plan that addresses drainage, ventilation, and flashing needs.
Step-by-Step Installation Guide
- Remove Old Roofing: Safely remove any existing roofing materials, ensuring the structure is intact and ready for the new roof.
- Inspect and Repair: Check the roof decking for damage. Replace any compromised sections to ensure a strong foundation.
- Install Underlayment: A protective underlayment should be applied to enhance water resistance before installing the metal panels.
- Attach Metal Panels: Begin the installation by placing the first panel at the peak of the roof and moving downwards, securing each panel with fasteners designed to withstand coastal conditions.
- Install Flashing and Trim: Flashing around edges, valleys, and penetrations is crucial, followed by installing trim to enhance waterproofing and aesthetic appeal.
- Final Inspection: Conduct a final walkthrough to ensure everything is properly installed and secure.
Safety Precautions during Installation
Safety should always be a priority during roofing installation. Proper safety gear, including helmets, gloves, and non-slip footwear, should be worn. Additionally, ladder safety practices must be followed, and working on roofs should only occur in safe weather conditions to prevent accidents.
Maintenance Tips for Coastal Metal Roofs
Regular Inspections and Repairs
To maximize the lifespan of coastal metal roofs, regular inspections are essential. Homeowners should annually check for signs of wear, rust, or loose panels. Any identified issues should be repaired promptly to avoid more significant problems in the future.
Cleaning Techniques to Avoid Corrosion
Routine cleaning is vital to remove salt and debris that can lead to corrosion over time. Using a soft-bristle brush and a mixture of water and a mild detergent is often sufficient. Avoid harsh chemicals that could damage the protective coatings found on quality metal roofs.
Maximizing the Lifespan of Coastal Metal Roofing
In addition to regular inspections and cleaning, applying a new protective coating or sealant every few years can significantly extend the roof’s life. Furthermore, ensuring trees and vegetation are trimmed back from roofs can prevent overhanging branches from damaging the roof or trapping moisture.
Cost Considerations and ROI for Coastal Metal Roofing
Initial Investment vs. Long-term Savings
While the initial cost of coastal metal roofing may be higher than traditional materials, the long-term savings can be substantial. Metal roofs are durable and energy-efficient, leading to lower cooling costs and reduced need for repairs.
Insurance and Warranty Factors
Homeowners should investigate insurance benefits associated with installing metal roofs, as many insurers offer discounts due to their resilience against extreme weather. Additionally, many manufacturers provide warranties that can cover material defects for decades, adding more value to your investment.
Increased Property Value with Quality Roofing
Investing in high-quality roofing can significantly raise your property value. A well-installed metal roof enhances curb appeal and attracts potential buyers, which can be especially beneficial in coastal areas where homebuyers look for durability and low-maintenance solutions.